The process of connecting an air compressor to a piping system may seem complicated to many users, but it’s not the case. Do you know how to connect your air compressor to a PVC pipe?
You need to connect a piping system to the air compressor to transport air to the intended tool or application. With improper PVC piping, your air compressor can fail. The compressed air can also leak.
Most users opt to connect a PVC pipe to their air compressors because it resists corrosion and is easy to cut and join. It is also readily available, affordable, and lightweight.
But it’s susceptible to explosion when subjected to high pressure. That’s why it’s advisable to use a PVC pipe only if your air compressor compresses up to 175 psi. Some PVC pipes may handle up to 600 psi but only when new.
To connect a PVC pipe to an air compressor correctly, use the following procedure:
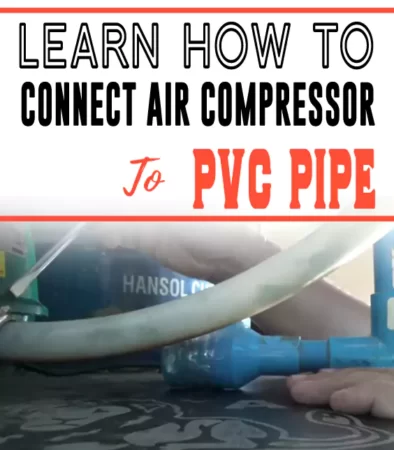
6 Steps to Connect Air Compressor to PVC Pipe
Step 1: Gather the Required Materials
The first step is to ensure that you have everything you require for the process. Search for all items and take them to your working area. You will require;
- PVC pipe
- An air compressor of 90 psi
- Clamps
- Connectors
- Couplers
- Brackets
- Tees
- Valves
If you don’t own an air compressor yet, check out our 120V air compressor reviews to find the best one for your needs.
Step 2: Set the Air Compressor
With all the items ready to use, you need to set up the air compressor to determine how the PVC pipe will run.
Place the air compressor strategically in your workshop to allow easy piping to various locations or applications.
The place you set the air compressor should be secure and have a power source.
Step 3: Start Connecting the PVC Pipe to the Air Compressor’s Valve
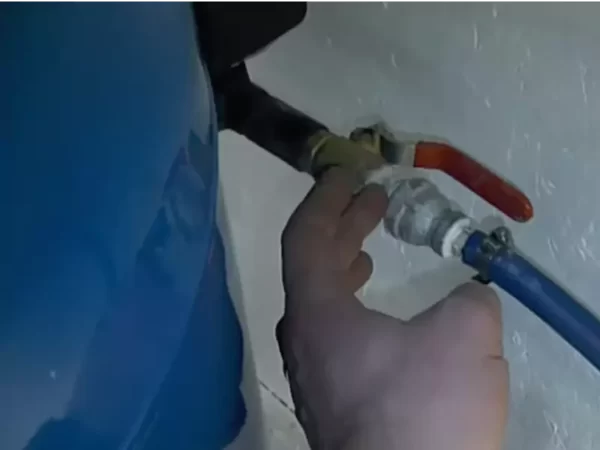
After setting up the air compressor, it’s time to start the pipe connection. The air compressor consists of a pipe connection valve.
Connect one open end of the PVC pipe to the valve. If difficult to connect, don’t force it. Use an ideal fitting connector to attach the pipe to the valve.
Then place a clamp on the tube around the connected area to hold it on.
Step 4: Connect the PVC Pipe to the Water Filter
When the pipe is secure at the air compressor’s valve, connect its other end to the water filter.
You may need to use a longer tube than the actual length from the compressor to the water filter.
It is because the air compressor vibrates a lot, loosening the fittings. As a result, you start experiencing air leaks. Also, the sound of the vibrating pipes may drive you crazy.
A longer pipe will reduce the noise and impact of the vibrations.
Step 5: Connect the Pipe to The Pressure Gauge
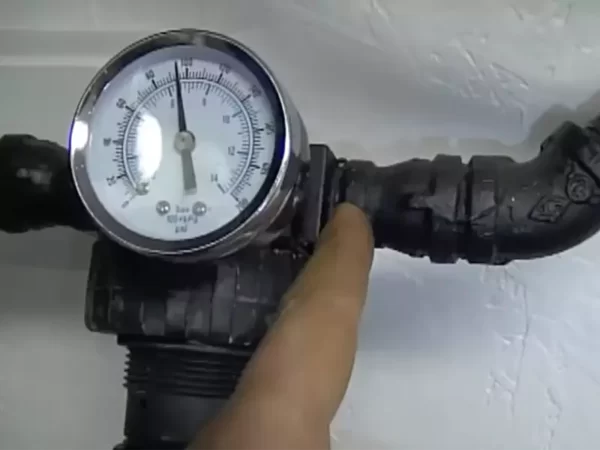
The water filter is next to the pressure gauge. Use an ideal connector and coupler to connect the two. It’s better if the fittings connecting the water filter and the pressure indicator are made with metal.
You may paint the metal part with a flat black rust paint to prevent it from corrosion.
In case you bang anything on them, the connection will not break. But if you use a PVC pipe to connect the water filter and pressure gauge, the likelihood of it breaking when subjected to pressure is higher.
Keep the gauge between 90 and 100 pounds pressure. Then continue with the piping. Take another PVC pipe and connect one of its openings to the pressure gauge.
Attach the PVC pipe to the gauge’s valve or with a reliable connector fitting. Put a clamp to hold it firmly.
Step 6: Align and Fix the Pipe within the Workshop
At this stage, you have already connected the PVC pipe with the air compressor, water filter, and pressure gauge.
Where you need the compressed air will determine how the pipe will run around your workshop or garage.
If the applications are nearby, there’s not much to do. You only need to ensure that the pipe from the pressure gauge can access the tool, device, or machine.
But if the application is far from the air compressor, you will need to set and fix the PVC pipe from the air compressor to the ideal location.
It would be best if you were careful where you place the PVC pipe as it’s delicate. The best place to set and fix it is along the room’s walls to the targeted location.
Follow the outline of your workshop or garage wall and set the pipe to follow. If the distance is too long, put some couplers in specific areas if you find it hard to tighten up the pipe properly with fittings.
Also, put brackets in certain areas to help secure the PVC pipe along the wall.
You may need to use many couplers and brackets to connect the air compressor to PVC. Luckily, they are very cheap and easily to find.
When branching off, use the tee. Ensure you connect the pipe tightly to prevent air leaks. Then continue fixing the PVC pipe in the direction of your targeted location.
Don’t forget to use the brackets and couplers for tightening up and securing the pipe in place. The piping will also look neat as everything will be well aligned and firmly placed.
Step 7: Prepare for future issues
Sometimes problems may occur along the PVC pipe. It’s wise to install valves at certain places along the pipe.
When there’s an issue, you don’t have to undo the entire piping system. You only need to close the valve and disconnect the tube in the area with the problem.
When connecting the valve to the pipe, ensure it fits firmly to prevent the compressed air from leaking.
Also, most valves have handles for closing and opening. Install the valve in a way that the handle stays at the side of the pipe. Otherwise, the valve handles may get in your way while working on the pipe.
Near the destination, install a tee. One line should go to the application or machine to be air compressed. The other extends a little. Place a cap on its end. In case you ever want to expand the piping, it will make it easy to do so.
After this, you will have successfully connected the air compressor with a PVC pipe.
As illustrated above, fitting an air compressor to a PVC pipe is not hard. But it may take much of your time, requiring you to be patient.
As earlier explained, though PVC pipe comes with many benefits, it’s not the ideal one to use with an air compressor. For your better understanding, here is a comparison of copper and PVC pipe.
PVC Pipe vs. Copper Pipe: Why Copper Pipe is better for Air Compressor
A PVC pipe can shatter when exposed to high pressure, posing a safety and health risk. Also, with age and a cold temperatures, a PVC pipe can become brittle.
It degrades with time, compromising its structural integrity. After some period, the pipe bursts, causing a lot of inconveniences and added expenses.
PVC pipes are also difficult to seal and install properly, causing a lot of leakage problems.
The PVC cement fails because if it doesn’t set correctly. Thread sealants frequently fail due to wrong application techniques.
Copper pipes are sturdy and long-lasting. You don’t have to worry about them exploding or degrading.
Also, a copper pipe does not corrode when condensation builds up. As a result, there’s no risk of any debris or particulates entering the system.
A copper pipe withstands heat very well and is aesthetically pleasing. The only disadvantage of copper pipe is the high cost.
Also, it requires skill and more time to solder copper pipe joints. It also requires a few more tools, such as a soldering kit*, butane fuel, and a pipe cutter.
Depending on your application, attaching an air compressor to a PVC pipe may not be safe. It would be better to dig deeper into your pockets and get a copper pipe than risking with a PVC pipe.
Conclusion
The information above illustrates that it’s not hard to connect the air compressor to PVC. What you require are the right tools, skills, and procedures.
Because the method requires substantial time, you will need to set aside a day for carrying out the process.
As discussed above, though there are PVC pipes designed to use with air compressors, they are not the best for high pressures, durability or cold temperatures.
A PVC pipe can break, causing injuries and harm to the air compressor and other things around.
Though copper pipes are expensive and require you to have the skill to solder the joints, they are best to use with an air compressor.
If you use a PVC pipe with your air compressor, it’s safe if the compressor is low psi, like below 175.
If you want to carry out the procedure for the first time, the above guide on how to connect the air compressor to the PVC pipe will help you. Follow each step, and you’ll nail it.
*Paid Link: As an Amazon Associate, I earn from qualifying purchases. Should you decide to purchase a tool through this link, I will get a small commission. The price of the tool won’t be any different to you.
Recent Posts
Many DIY lovers and engineers want to build something cool in their garages. What's cooler than a kit airplane? In this setup, the builder receives parts and puts them together in their own space....
Diamond blades have various uses, from cutting tiles and glass to cutting gems and semiconductor materials. If you’re planning to start a renovation or building project, you’ll need a diamond...